A Comprehensive Guide to the Process and Benefits of Plastic Extrusion
In the substantial world of manufacturing, plastic extrusion arises as a necessary and extremely efficient process. Translating raw plastic into continual profiles, it provides to a huge selection of sectors with its impressive versatility.
Comprehending the Essentials of Plastic Extrusion
While it might show up complex initially look, the process of plastic extrusion is basically easy - plastic extrusion. It is a high-volume production method in which raw plastic is melted and formed right into a continuous profile. The procedure starts with the feeding of plastic product, in the type of granules, pellets, or powders, right into a heated barrel. The plastic is then thawed making use of a mix of warmth and shear, applied by a revolving screw. As soon as the molten plastic gets to completion of the barrel, it is compelled via a small opening called a die, forming it right into a desired type. The designed plastic is then cooled, strengthened, and reduced into wanted lengths, finishing the process.
The Technical Refine of Plastic Extrusion Explained
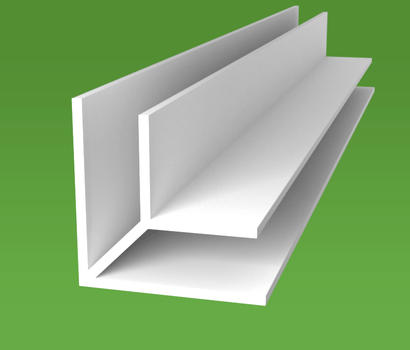
Kinds Of Plastic Suitable for Extrusion
The choice of the best kind of plastic is a vital element of the extrusion process. Different plastics use unique residential or commercial properties, making them much more fit to specific applications. Understanding these plastic types can significantly enhance the extrusion procedure.
Contrasting Plastic Extrusion to Various Other Plastic Forming Approaches
Comprehending the sorts of plastic appropriate for extrusion paves the method for a wider discussion on exactly how plastic extrusion stacks up versus various other plastic forming approaches. These include shot molding, blow molding, and thermoforming. Each approach has its distinct usages and advantages. Shot molding, as an example, is outstanding for creating detailed components, while blow molding is perfect for hollow things like containers. Thermoforming excels at forming large or shallow components. Plastic extrusion is unmatched when it comes to creating constant accounts, such as pipelines, gaskets, and seals. It also allows for a consistent cross-section along the size of the product. Thus, the selection of technique largely depends upon the end-product requirements and specs.
Trick Benefits of Plastic Extrusion in Manufacturing
In the realm of production, plastic extrusion supplies many considerable advantages. One noteworthy benefit is the cost-effectiveness of the procedure, which makes it an economically appealing production approach. Additionally, this strategy gives premium item adaptability and boosted manufacturing speed, thus enhancing general manufacturing efficiency.
Economical Manufacturing Approach
Plastic extrusion jumps to the center as an affordable manufacturing method in production. Furthermore, plastic extrusion requires much less power than typical manufacturing approaches, adding to lower functional prices. In general, the monetary benefits make plastic extrusion a highly YOURURL.com appealing choice in the manufacturing industry.
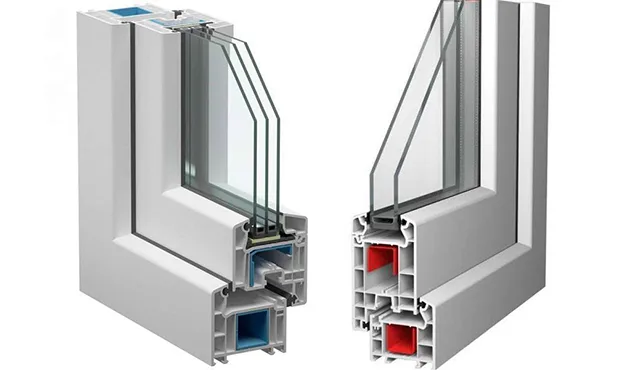
Superior Product Versatility
Beyond the cost-effectiveness of plastic extrusion, one more substantial advantage in making lies in its exceptional item versatility. This makes plastic extrusion a perfect option for industries that call for customized plastic parts, such as automotive, building, and product packaging. In essence, plastic extrusion's item adaptability promotes technology while boosting functional efficiency.
Boosted Production Speed
A substantial advantage of plastic extrusion exists in its enhanced manufacturing rate. Couple of various other manufacturing processes can match the speed of plastic extrusion. Furthermore, the ability to keep regular high-speed manufacturing without giving up item quality establishes plastic extrusion apart from various other methods.
Real-world Applications and Influences of Plastic Extrusion
In the world of manufacturing, the technique of plastic extrusion holds profound value. This procedure is widely used in the production useful content of a selection of items, such as plastic tubing, home window frameworks, and weather condition removing. Consequently, it significantly affects industries like construction, product packaging, and vehicle markets. Its effect prolongs to daily items, from plastic bags to tooth brushes and non reusable flatware. The financial advantage of plastic extrusion, largely its cost-efficient and high-volume outcome, has changed manufacturing. The ecological influence of plastic waste remains a worry. The industry is persistently aiming for developments in naturally degradable and recyclable materials, showing a future where the advantages of plastic extrusion can be maintained without jeopardizing environmental sustainability.
Verdict
Finally, plastic Continued extrusion is a effective and very efficient approach of transforming raw products right into diverse products. It offers many advantages over various other plastic forming approaches, including cost-effectiveness, high output, minimal waste, and layout flexibility. Its effect is exceptionally felt in different markets such as construction, auto, and consumer items, making it a pivotal process in today's production landscape.
Digging deeper into the technological process of plastic extrusion, it starts with the choice of the appropriate plastic product. When cooled down, the plastic is cut into the needed sizes or wound onto reels if the item is a plastic movie or sheet - plastic extrusion. Contrasting Plastic Extrusion to Various Other Plastic Forming Methods
Recognizing the kinds of plastic appropriate for extrusion leads the way for a broader conversation on exactly how plastic extrusion piles up versus various other plastic developing techniques. Few other production processes can match the rate of plastic extrusion.