A Comprehensive Overview to the Refine and Advantages of Plastic Extrusion
In the vast world of manufacturing, plastic extrusion arises as a essential and very efficient procedure. Transmuting raw plastic right into constant accounts, it deals with a huge selection of industries with its impressive flexibility. This overview aims to clarify the detailed actions associated with this approach, the sorts of plastic suitable for extrusion, and the game-changing benefits it brings to the market. The following discussion guarantees to unfold the real-world influences of this transformative process.
Recognizing the Essentials of Plastic Extrusion
While it might appear complex at initial glimpse, the procedure of plastic extrusion is fundamentally simple. The procedure starts with the feeding of plastic material, in the type of pellets, granules, or powders, into a warmed barrel. The designed plastic is after that cooled, strengthened, and reduced into preferred lengths, finishing the procedure.
The Technical Process of Plastic Extrusion Explained
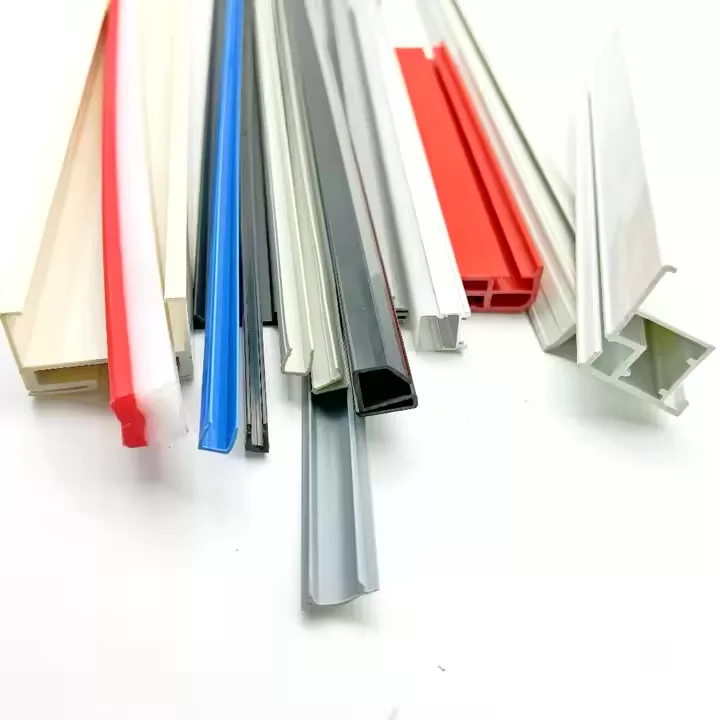
Kinds Of Plastic Suitable for Extrusion
The choice of the ideal kind of plastic is an essential element of the extrusion procedure. Different plastics use unique homes, making them much more suited to particular applications. Comprehending these plastic types can substantially enhance the extrusion procedure.
Comparing Plastic Extrusion to Other Plastic Forming Approaches
Comprehending the sorts of plastic appropriate for extrusion leads the way for a wider discussion on how plastic extrusion compares to various other plastic forming approaches. These include shot molding, impact molding, and thermoforming. Each technique has its unique usages and benefits. Injection molding, for example, is exceptional for developing intricate components, while strike molding is excellent for hollow objects like bottles. Thermoforming excels at developing superficial or large parts. Plastic extrusion is unequaled when it comes to developing continuous profiles, such as gaskets, pipes, and seals. It likewise permits for a consistent cross-section along the length of the product. Hence, the selection of approach mainly depends on the end-product needs and specifications.
Key Advantages of Plastic Extrusion in Production
In the world of manufacturing, plastic extrusion offers lots of substantial advantages. One noteworthy benefit is the cost-effectiveness of the procedure, which makes it an economically appealing manufacturing approach. Furthermore, this method offers premium item adaptability and boosted production rate, therefore increasing total production efficiency.
Affordable Production Approach
Plastic extrusion jumps to the leading edge as a cost-effective manufacturing method in manufacturing. This process sticks out for its ability to produce high quantities of material quickly and effectively, giving makers with substantial cost savings. The primary price advantage is the capacity to utilize much less expensive basic materials. Extrusion uses polycarbonate products, which are less pricey contrasted to ceramics or steels. Additionally, the extrusion procedure itself is relatively easy, lowering labor expenses. In addition, plastic extrusion requires much less power than traditional production approaches, contributing to reduced operational expenses. The process additionally minimizes waste, as any type of excess or malfunctioning products can be reused and recycled, offering one more layer of cost-effectiveness. On the whole, the financial benefits make plastic extrusion an extremely appealing alternative in the production industry.
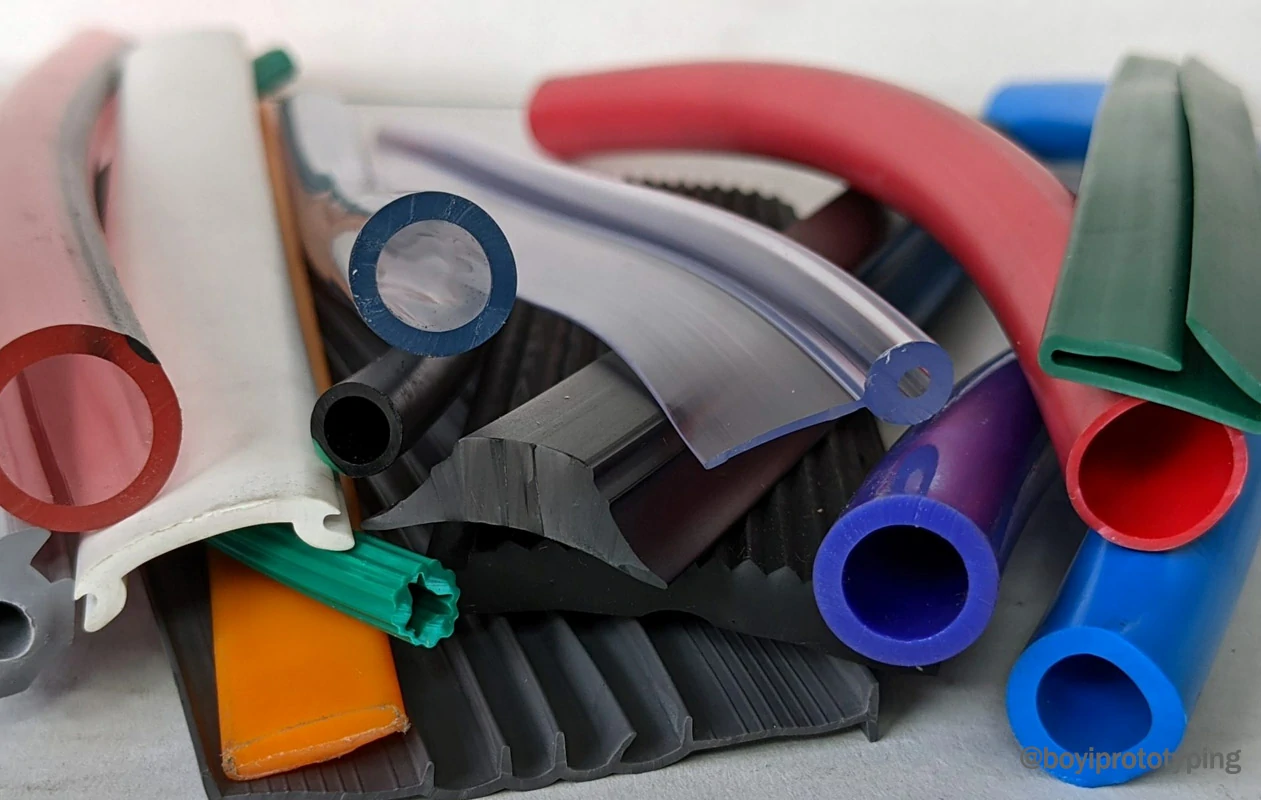
Superior Product Versatility
Beyond the cost-effectiveness of plastic extrusion, one more considerable advantage in manufacturing depend on its superior item versatility. This procedure enables the creation of a wide variety of products with differing forms, styles, and sizes, from straightforward plastic sheets to intricate accounts. The adaptability is associated to the extrusion pass away, which can be customized to produce the wanted product layout. This makes plastic extrusion an ideal remedy for markets that require tailored plastic elements, such as automotive, building and construction, and product packaging. The ability image source to generate diverse products is not just helpful in meeting details market demands but additionally in allowing suppliers to explore brand-new line of product with very little capital expense. Fundamentally, plastic extrusion's product versatility promotes development while boosting operational performance.
Improved Manufacturing Speed
A substantial advantage of plastic extrusion lies in its improved production rate. Few other manufacturing processes can match the rate of plastic extrusion. In addition, the capacity to maintain regular high-speed production without sacrificing item high quality sets plastic extrusion apart from various other methods.
Real-world Applications and Influences of Plastic Extrusion
In the realm of manufacturing, the strategy of plastic extrusion holds extensive importance. This process is commonly utilized in the production of a selection of products, such as plastic tubes, home window frames, and weather removing. Therefore, it considerably influences sectors like building and construction, product packaging, and automobile sectors. Its effect extends to day-to-day items, from plastic bags to tooth brushes see this and disposable flatware. The economic benefit of plastic extrusion, largely its high-volume and cost-efficient output, has blog here actually changed production. However, the ecological influence of plastic waste remains a worry. Therefore, the industry is persistently striving for innovations in biodegradable and recyclable materials, showing a future where the advantages of plastic extrusion can be kept without compromising environmental sustainability.
Final thought
To conclude, plastic extrusion is a extremely effective and effective method of changing raw materials right into diverse items. It provides numerous benefits over other plastic creating approaches, including cost-effectiveness, high outcome, very little waste, and design flexibility. Its impact is exceptionally really felt in different sectors such as building, automotive, and consumer items, making it a critical process in today's manufacturing landscape.
Diving deeper into the technical procedure of plastic extrusion, it starts with the choice of the proper plastic material. As soon as cooled, the plastic is reduced into the required sizes or injury onto reels if the product is a plastic film or sheet - plastic extrusion. Comparing Plastic Extrusion to Other Plastic Forming Techniques
Understanding the kinds of plastic ideal for extrusion paves the means for a wider discussion on how plastic extrusion stacks up against various other plastic forming methods. Few other production procedures can match the speed of plastic extrusion.